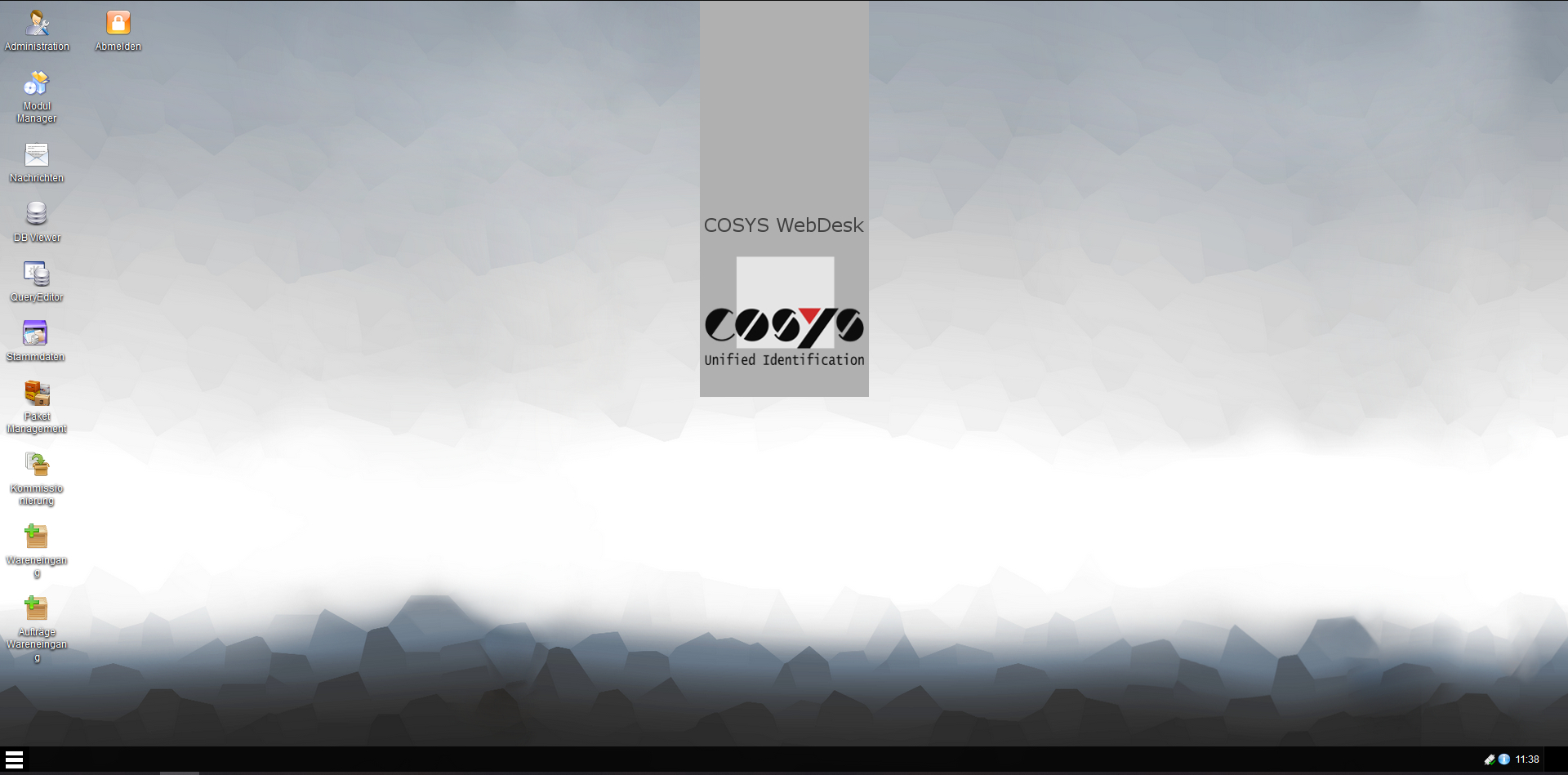
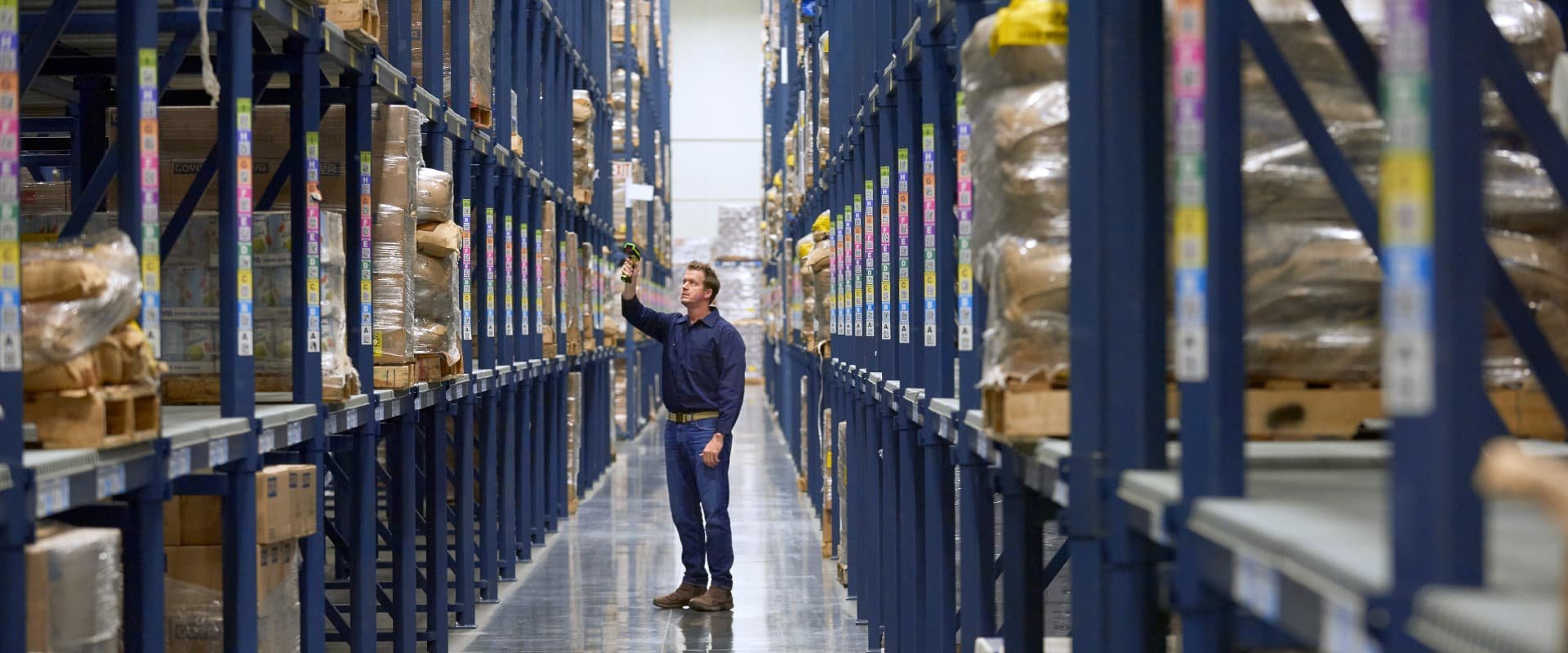
Wholesale & Warehouse Software Modules
Time never stands still. Somewhere, a customer is always waiting for his delivery. Providing the right goods, in the right quantity, at the right time requires processes that mesh seamlessly. Mobile access to up-to-date and reliable information is indispensable. We have been developing mobile software solutions for over two decades, with the aim of making warehouse processes simpler and more efficient. We map the business processes of your enterprise resource planning in a mobile-friendly way.Wholesale / Warehouse Backend and Mobile Modules
Wholesalers thrive on stock and fast delivery options to specialist dealers, craftsmen, etc.. As the main customer of the producers, wholesalers refine the products with the consulting service, delivery availability and other services and market them further.
Without software, nothing works in wholesale for a long time! Anyone who wants to deliver reliably uses COSYS software.
Managing your own inventory requires warehouse management software.
Small specialized niche wholesalers also need small business warehouse management software.
As a building materials dealer, do you deliver your craftsmen to the customer´s construction site? Then our transport software helps you to record the entire delivery process, from loading to delivery and return.
Do you set up consignment stores for your customers? Then your customers should record the consumption as a repeat order via barcode scanner and report it directly via OnlineOrder.
A wholesale trade lives from high stocks, so every inventory is a feat! But with the COSYS inventory software and rental equipment, it succeeds flawlessly.
Our software solutions map your business process, you use the modules you need, later you can add more modules and functions, here is a short outlook:
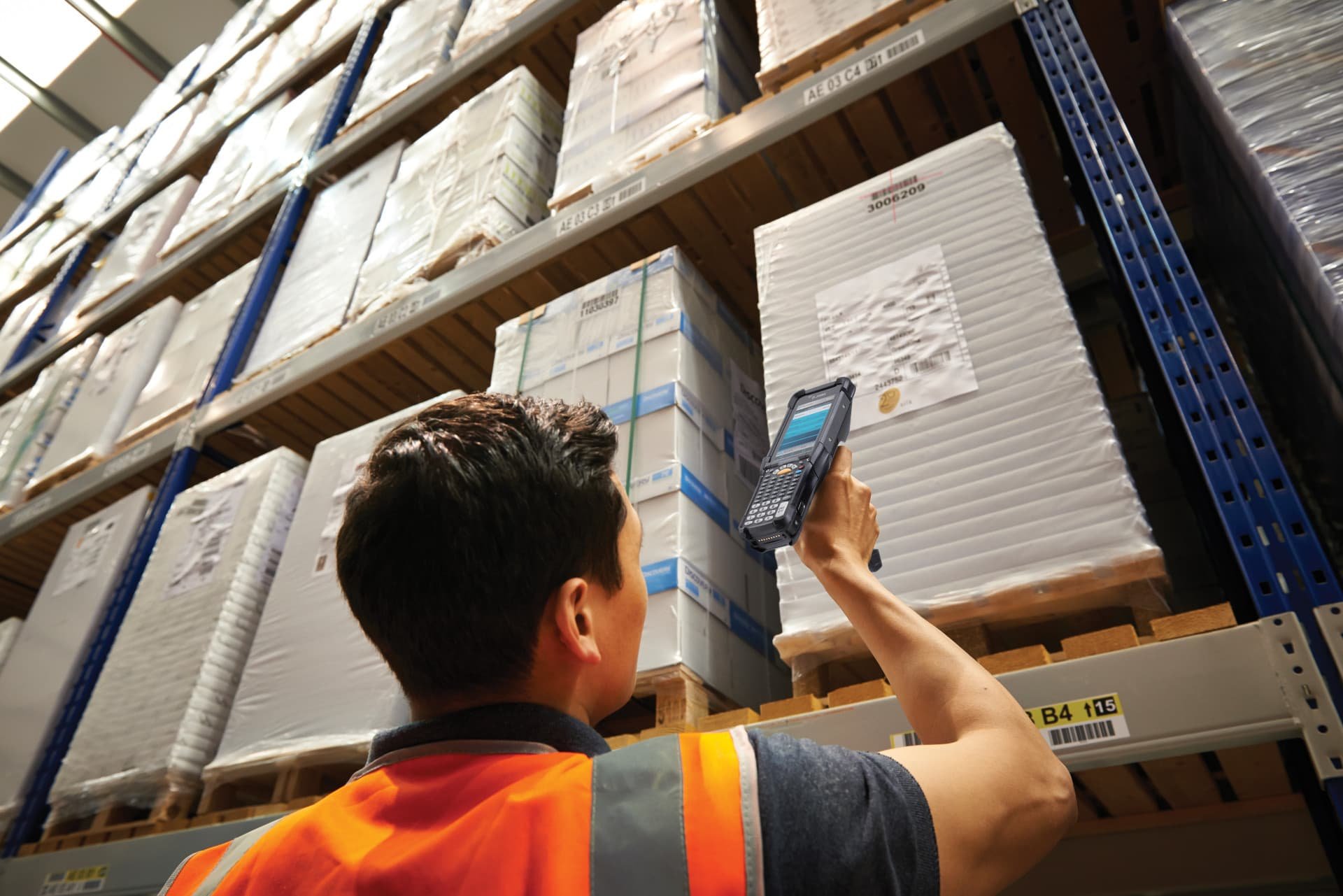
The Warehouse Management Software is designed for companies that want to perform an accurate work process. With the help of the COSYS Warehouse Management Software, all warehouse activities are fulfilled, recorded via MDE and booked in the warehouse management system. There is a data exchange with your ERP system and you have a transparency about the current processing status.
COSYS´ Warehouse Management Software offers strong modules to meet and continuously optimize your internal business processes and the necessary industry requirements.
More about Warehouse Management Software
Your company is growing, is a healthy medium-sized enterprise and is looking for a solid warehouse management software in addition to the ERP system? Then our powerful modules help to improve exactly those work processes that the ERP currently covers only incompletely. If incoming goods are usually booked in late, the mobile app helps to digitally display the information to the employee, the employee can perform the incoming goods inspection via scan and transfer the data to the ERP system by completing the order in the app. Further advantages arise within the stock transfer, picking, shipping, inventory, etc.
More about Warehouse Management Software for Small Business
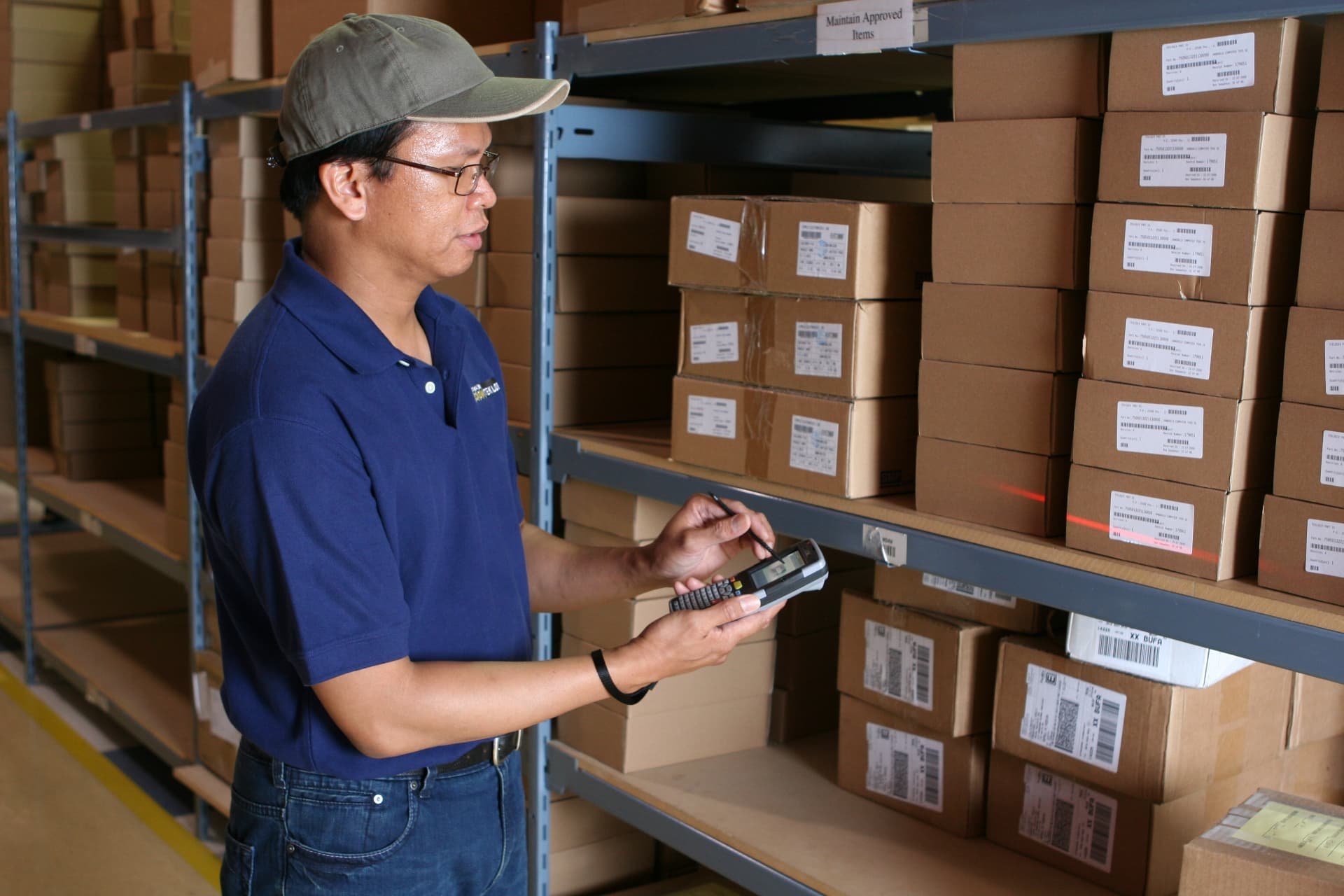
Transport software
You may supply your customers up to the last mile, bring your wholesale assortment up to the specialized trade or to the construction site of the craftsman? Then error-free loading is important, in which the loading equipment is recorded in addition to the picked packages. During the tour, the software shows you the customers you need to approach and helps you find your way thanks to the map function. During the delivery it is ensured that all packages are delivered and are acknowledged at the destination by photo and signature. Separate contact persons, parking permission, acceptance refusal and the loading equipment management are only some of the further functions of our transport software.
OnlineOrder
The reorder solution for wholesalers helps to capture the consumed material by barcode and transfer it to the wholesaler, who performs the invoicing of the consumption as well as the re-delivery of the material.
COSYS inventory software and loaner devices
The accurate recording of actual stocks is the task of the inventory. Instead of using pen and paper, you work with a mobile app on an MDE device or smartphone to record item by item. In the COSYS backend, the recorded data can be evaluated, difference lists can be created and the inventory can be edited.With all these challenges, the COSYS software helps you, the optimal software for wholesale!
Wholesale barcodes
Barcodes help goods to be handled quickly and identified unambiguously. Scanning the items against the supplier order or the sales order with a barcode reader helps to avoid mix-ups and to quickly book in and distribute the goods.
Why do I need another software besides ERP?
Every wholesaler has a specialized merchandise management and ERP system tailored to its industry. The warehouse and transport processes attached to it can best be mapped with COSYS software, as this is geared towards the efficient, targeted and error-free execution of tasks.
The COSYS software exchanges data with the ERP, the data is managed centrally in the ERP and you benefit from the fact that your employees can see the latest data directly in the warehouse and transport process in a mobile app on the smartphone and/or MDE device, record data, these can be plausibility checked and posted in real time.
What are the major challenges facing wholesalers?
Shortage of personnel, work processes have to be carried out more efficiently because fewer personnel are available.
Customer request for short delivery time, large assortment, high delivery availability,
Cost pressure, customer requirements lead to costs and require lean internal processes
Company-critical data can be viewed on the move
Inventory data can be collected
Through the COSYS WebDesk overview of the processing status
Inventories can be viewed digitally and reported back to the ERP system in real time
Digitization of business processes
Less time delay because the inventories are recorded directly
Custom configuration maps the wholesaler´s individual process
Reduction of search times in the warehouse
Higher availability of goods
Less article mix-up through the use of barcode capture
Reduction of the error rate
Wholesale and warehouse Android software modules
COSYS offers mobile software modules for all business processes to enable time savings and transparency. Software modules can be configured customer-specific.
If you decide to add more modules later, the modules can simply be purchased in addition.
Wholesale & Warehouse Software FAQ
The COSYS software is basically modular to allow for later expansion of the software. In addition to the wholesale software, COSYS can also make use of mobile hardware from COSYS, i.e. buy, borrow or lease devices. This gives wholesalers a central point of contact for digital processes with comprehensive services and support.
In the SHK sector, many wholesalers already work with the COSYS software. Different company structures, internal processes and special services result in basically similar workflows, processes and requirements. Nevertheless, customer-specific processes can also be mapped by configuring the software through COSYS.
The printed EAN code can also be used as a reference to an article. Provided that the number sequences of the EAN/manufacturer article number(s) are managed in the master data, the PDC software can reference a wide variety of fields and thus identify the article by the EAN and also other article numbers. This functionality reduces costs, as the creation of own labels can be omitted. The recording of the goods receipt is also considerably easier, as the article can be clearly recorded under a wide variety of designations.
The COSYS software is configured customer specific. Usually there are one or a few processes that cause an above-average number of problems and require a lot of time. These business processes, such as goods receipt or returns recording, can already be implemented in a first small sub-project - without starting directly into a large project. By operating a first process, the employees already get used to the MDE systems and also recognize the advantages for themselves. Further processes are thus supported by the employees and basic business logics can already be built upon.
C-parts are existentially important for producers, craftsmen and end users. Despite their importance, supply by wholesalers must be cost-efficient and fast. The customers´ reordering process can already be used to map this efficiently and digitally. Your customers can already use MDEs to record the materials they have used and the wholesaler can arrange for subsequent delivery.
DIY stores expect their suppliers to deliver orders promptly, correctly and pre-sorted. This pre-sorting must be carried out on the basis of shipping units so that the distribution center can quickly distinguish whether the shipping unit is a store delivery or a warehouse delivery in order to enable fast handling. To ensure that this picking process can take place without errors, a well-sorted warehouse with digital goods receipts is required in advance.
Flexibility is part of the business model and therefore returns can also be recorded. This is usually referenced to a delivery order, so the employee sees which items were sent to the customer and records the returned parts. Depending on the type, parts must be checked according to quality assurance or end up back in the warehouse as an addition after visual inspection.
Inventories are a burdensome duty that are required by law. Nevertheless, an inventory must be carried out and it creates a valid data basis about the stocks. It makes little sense to only check whether the book inventory is also available, but to count with open eyes what is available. High inventory costs are incurred due to the downtime of productive business operations and the many hours spent on rework. For example, paper-based inventory lists must be evaluated, entered into the ERP system, and then the difference list must still be printed out and cross-checked again. Instead, a digital inventory solution from COSYS provides the ability to quickly and easily count area by count area using loaner equipment. The results also produce a difference list that can then be recounted by a secondary counter. This results in fewer interruptions to business operations and reduced rework time.
There are a few ways in which you can optimize the warehouse. First of all, it is important to make sure that all the shelves are neatly placed and all the items are properly labeled. This way you can quickly and easily see where everything is and what you need. Barcodes, which are already applied to over 90% of products, help to further optimize the process. Storage locations can also be labeled with them, helping to avoid confusion in the warehouse and keep accurate inventories. Additionally, it can be helpful to use inventory management software. This software allows you to accurately manage and monitor your warehouse. Items can be easily created, inventory can be viewed, and you can set notifications to reorder in a timely manner.
Warehouse organization - our software is the perfect solution! Our software is quick to set up and can help you organize your warehouse more efficiently. We have a lot of experience in warehouse organization and can offer you the perfect solution for your business. Our software will save you time and effort in organizing your warehouse. You will be amazed how easy and fast our system is.
Inventory is the number of a company´s goods that are for sale. This includes both physical goods and digital products. The level of inventory is determined by the demand and sales of the products. Companies usually try to keep their inventory as low as possible to save costs. If a company operates its own production, safety stocks still ensure that production can continue permanently to avoid costly interruptions.
There are a few ways to reduce inventory. First, you can try to keep the products you sell most often at the top and push those that sell less often to the back. This way, you can make sure you always have enough products on hand without cluttering up your warehouse. A smaller assortment lowers costs. Another option is to review your order quantity and reduce it if necessary. For example, if you find that you are only selling an average of 10 pieces of a particular product per month, you could try reducing your order to 5 or even 3 pieces per month. This way, your warehouse will stay empty and there will be less waste. Also, there is the possibility to lower the risk of inventory, for example, by setting up a consignment warehouse, this way the goods are physically in your warehouse and you only pay when you use the material.
Average inventory varies by company and industry. In general terms, average inventory is a combination of the value you hold for your business and the risk you are willing to take. There are several ways to calculate average inventory. One method is to average it over a period of time. This can be a year, a quarter, or a month. Averaging gives you an indication of the typical inventory levels in your business. Another method is to calculate the optimized inventory level. This level varies depending on what variables you include in the calculation. For example, you can calculate the optimal inventory level of stocked goods so that you minimize inventory holding costs and supply chain outages. If you think your current inventory is below the average level, you can consider ordering more stock items. On the other hand, if you think your current inventory is above the average level, you can consider ordering fewer stock goods.
Inventories are a burdensome duty that are required by law. Nevertheless, an inventory must be carried out and it creates a valid data basis about the stocks. It makes little sense to only check whether the book inventory is also available, but to count with open eyes what is available. High inventory costs are incurred due to the downtime of productive business operations and the many hours spent on rework. For example, paper-based inventory lists must be evaluated, entered into the ERP system, and then the difference list must still be printed out and cross-checked again. Instead, a digital inventory solution from COSYS provides the ability to quickly and easily count area by count area using loaner equipment. The results also produce a difference list that can then be recounted by a secondary counter. This results in fewer interruptions to business operations and reduced rework time.
The stock is checked using a scanner that captures the barcodes on the products. This scanner is connected to our COSYS software so that the current stock level can be displayed at any time. The process is quick and easy and allows us to know the exact stock.
There are some important principles that should be followed when storing goods. Firstly, it is important that the goods are properly labeled and marked so that they can be easily found later. Secondly, it is important to store the goods in a dry and clean place to avoid mold or other damage. Some goods must be stored separately, others in cold storage. The goods do not get better the longer they lie, so regular stock rotation should be aimed for.
Are you interested in a wholesale & warehouse software and still need help. We will gladly advise you further and answer all your questions!
Contact request