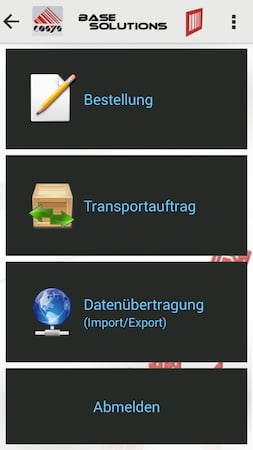
Order
The two modules "Order" and "Transport order" map the necessary steps of demand generation and goods transport. The third module "Data transmission" is used by employees when only parts of the warehouse are illuminated with WLAN.
In the area of automotive manufacturers, COSYS is strong in the logistic areas: production, warehouse management, intralogistics for in-house mail and inventory. For almost 4 decades, COSYS has been developing software solutions that are specifically adapted to the requirements of the automotive industry. In addition, COSYS offers the appropriate MDE hardware such as MDE devices, handheld scanners or label printers.
The framework of COSYS software solutions consists ofSoftware modules. Each module captures a logistical process. The module itself is already in place and is only filled with specifics of the automotive industry. Our industry configuration includes batch management, serial numbers, component tracking and other functions available on request. Data between ERP systems and the COSYS solution is exchanged via standardized interfaces.
WithoutHardware no software runs. That is why COSYS has a specialized technical department that knows everything about MDE devices, repairs and advises. With us you can purchase new equipment, buy used, lease equipment permanently or for a time, leave old equipment as a deposit and much more.
When purchasing new equipment through COSYS, you can secure your investment with additional agreements. We will discuss with you which services are included in these agreements. Possible are: Additional devices, for example, for inventory, replacement devices in case of failure and repair of the damage and remote assistance in case of problems on site.
The production chain at automotive manufacturers is long. It´s not a matter of sticking two parts on top of each other and putting things in an outer box. Many production steps are necessary until a finished car is at the end of the chain. Record the individual production steps with COSYS mobile software. Both components and batches are tracked via the mobile software and this data is digitally prepared in the COSYS WebDesk. If you need further data for your track and trace in production, we will integrate it.
Capturing barcodes before and after production steps is accurate and does not take long. With each scan, the software checks whether the corresponding items are intended for the following production step. If not, the employee receives error messages.
Your ERP system does not provide all the data you would like to have for production? The COSYS WebDesk displays both the master and article data from your ERP system as well as all mobile data. The tabular structure is very clear in the COSYS WebDesk. In addition, you can define the views in WebDesk yourself: Which columns do you want to show? Which contents are at the front? According to which values do you want to sort? For each column value there are filter fields to search specifically for status, article, order numbers and other data.
Only one BOM component is missing to put everything together? Avoid such scenarios and order intelligently. COSYS Online-Order App bypasses all the ways you have to do with an ERP system: write or call the purchasing department, confirm three times which article and in which quantity you need, go through release processes and so on. The employee only has to enter the articles via barcodes, enter the quantity and, if necessary, add a comment to the order. This data is then automatically transferred to the ERP system and processed there.
Many automotive manufacturers produce just-in-time or just-in-sequence. The storage areas have thus become smaller and depend on maximum efficiency. This efficiency begins with goods receipt, in that only the ordered goods are actually accepted in perfect condition. After that, it is important to store the goods skillfully. Do not leave it to chance but to our software to store parts for production hall A near exit A, for hall B near exit B and so on.
Mobile software:For complex warehouse management, COSYS offers several modules that are adapted to your processes. Because we configure instead of program, we can implement projects quickly and provide demo versions for testing in advance.
If your leading system is an ERP system, the first priority is real-time data exchange. This data exchange ensures that the inventories on site in the warehouse and production match those in the ERP system. No more discrepancies between physical and system inventory. COSYS has already developed interfaces to ERP systems such asSAP, Microsoft DynamicsAX, Microsoft DynamicsNavisionweclapp. So when your warehouse worker takes an order at the receiving dock, all current order numbers are on COSYS mobile software including expected items.
The following warehouse modules are available for you to choose from: Goods Receiving, Putaway, Stock Transfer, Returns, Picking and Shipping Control. Within these modules there are functions such as: Enter NVEs, track loading equipment, scan batches and serial numbers, FIFO, take photos, manage parts lists and more.
Backend:An ERP system that provides everything a warehouse manager needs. That has yet to be invented. So use the COSYS WebDesk. This management tool is included in the COSYS backend. The clear and tabular views reveal all the warehouse data and order status you need. You want to know how many picking orders are open for production hall A? Just filter by the customer, in this case production, and the WebDesk shows you with self-explanatory icons what the statuses are: open, partially processed, finished, missing or damaged.
Production stalls because it takes far too long to communicate from the warehouse that parts are damaged? This does not happen with COSYS. You can store comments in every module. In case of comments such as "damaged" or "out of stock", the software automatically sends an e-mail to the responsible person so that it is taken care of immediately.
The larger the car plant, the more time goes into internal organization. In-house mail is a big factor in this internal organization. COSYS Package Inhouse Software takes a lot of work off your employees´ hands, eliminates errors and automates many steps of in-house mail distribution.
Typical steps in in-house mail distribution are parcel acceptance, parcel assignment and delivery or self-collection. COSYS Package Inhouse covers these steps. The employee scans with his handheld the
delivered parcels and obtains a digital signature from the CEP service at the end. Then he assigns the parcels to the employees in another module. During the assignment, e-mails can already be sent automatically to the employees so that they know that their mail is there.
Every company delivers internal mail differently. Some have a fixed in-house mail storage location, perhaps per building, where everyone picks up their mail. Others bring the parcels to the office. COSYS software can and knows all delivery types and maps these types in a streamlined way.
Not only does COSYS Package Inhouse map all package statuses, the software is particularly intuitive. A clear main menu leads to the modules, which in turn require as much data as necessary and as little as possible. Our freeDemo app for in-house mail distribution shows how understandable and self-explanatory COSYS software is.
Status viewCapturing data on mobile devices is all well and good, but managing and controlling it is where success lies. COSYS WebDesk tabulates what each shipment status is. You can filter by employee, search by shipment number or view only the packages with the status "arrived". These filters allow you to search for important information and answer questions about the shipment status at a glance.
Inventory needs more employees than usual, often too much time, more equipment than usual and software. We can not serve you with employees, but everything else you get through COSYS. Be it 3 additional devices for the one inventory day, a software in addition and the time you get indirectly, because inventory with COSYS is much faster.
The time saved in inventory starts with the delivery of the devices. When you order software and hardware from COSYS, these devices are ready for immediate use: software is installed, user data is stored and master data is imported. The
intuitive software ensures a quick count and inventory. Finally, the COSYS backend synchronizes the mobile-captured data with your ERP system and outputs ready-to-use inventory reports if required. That doesn´t just sound simple, it is.
As with the house mail distribution, you will also be able to take inventory in the GooglePlay Store and AppleApp Store found what you are looking for. For both operating systems we have a freeDemo app of our inventory software.
automatic reordering via online order
Record NVEs and own containers and loading equipment
Certified cloud backend with various interfaces
Automatic e-mail dispatch in case of shortages and damages
Define barcode types and required information yourself
No delays in production
Record data according to internal specifications
Save manpower with internal organization
ERP system receives all current data
Digital and complete documentation of all work steps
COSYS offers a wide range of complete solutions consisting of software, hardware and related services for the automotive industry. COSYS complete solutions enable the digitalization and expansion of resource distribution of a wide variety of work steps along the flow of goods.
Management or post-processing of the recorded data can be carried out in COSYS´ own back-end, the COSYS WebDesk. By regularly scanning the article codes in various work steps, a complete history of the goods movement can be ensured.
Component tracing
Production order solution
Warehouse management software solution
Online order
Inventory / Inventory
Package Inhouse
Hardware service
Everything you provide us with. You need batches? Then we add a (scan) field for batches. Need to track your containers? Then either scan the serial number or select containers via drop-down and so on.
In an initial conversation, you clarify initial questions with our sales representative. Then you will receive an offer and, if required, a free trial version of the discussed solution. In a workshop, the final details are also clarified.
The data is stored in the backend. When we install the backend on your server, your IT takes over the backup. In the COSYS Cloud, we ensure that data is not lost and is always accessible.
No. A maximum of two users are usual for the COSYS WebDesk, i.e. the web-based administration interface. With regard to the mobile app, the number of users varies from customer to customer.
COSYS digitizes your logistics data and this has several advantages: always up-to-date and retrievable data, fewer errors in the operational area, faster processes, 100% traceability, progress histories and much more.
Chat with us, email us - more formally - using the contact form, or call us directly to learn more.
COSYS Lebensmittelhandel Branche
COSYS Parfümerie / Beauty Branche
COSYS Tabak Branche
COSYS Blumengroßhandel / Blumengeschäft Branche
COSYS Convenience Store Branche
COSYS Sanitärgroßhandel / Baustoffhandel Branche
COSYS Technischer Handel Branche
COSYS Schiffbau und Werften Branche
COSYS Speditionen / Paket Dienste Branche
COSYS Versandhandel Branche
COSYS Automobilindustrie Branche
COSYS Automobilzulieferer Branche
COSYS Elektroindustrie Branche
COSYS Maschinen- und Anlagenbau Branche
COSYS Pharmaindustrie / Pharmagroßhandel Branche
COSYS Baumärkte / Baufachhandel Branchen
COSYS Spielwaren Großhandel / Spielwarengeschäft Branche
COSYS Leder & Schuh Branche
COSYS Schraubenhandel / Schraubenhersteller Branche
COSYS Textilgroßhandel und Einzelhandel Branche
COSYS Logistik- und Postunternehmen Branche
COSYS Messen Branche
COSYS Flughäfen Branche
COSYS Schienenfahrzeuge Branche
COSYS Kliniken Branche
COSYS Behörden Branche