
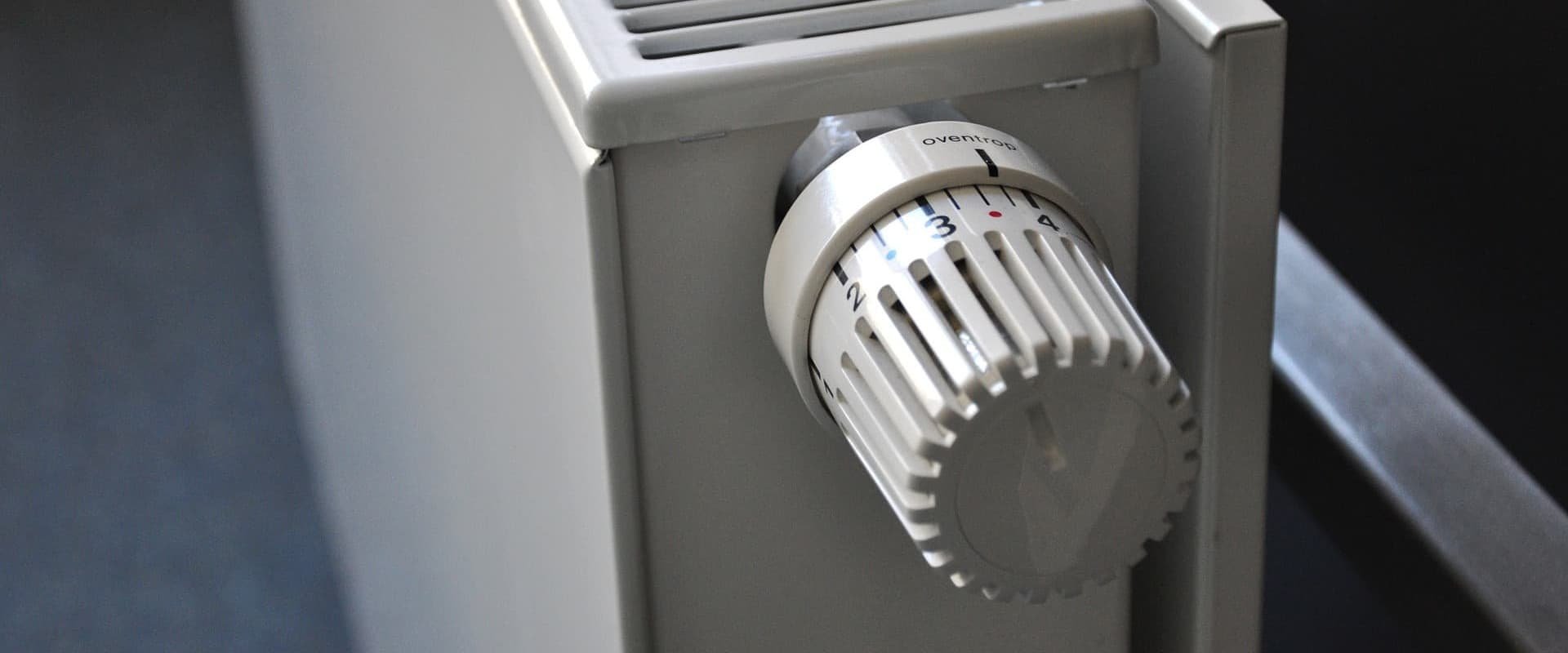
Wholesale plumbing supplies / building materials trade
Wholesale plumbing supplies and building materials retailers improve their business by making warehousing, transport and other logistics processes digital. COSYS develops software solutions that digitize everything from goods receipt, reorders, customer delivery and inventory.Digitization for heating, sanitary and building materials trade
Digitization requires three things: mobile software for warehouse workers, craftsmen and drivers, insight into real-time inventories and tours for planning, and suitable hardware to run the whole thing. At COSYS, you´ll find all three. Our mobile software is hands-on and thrives on numerous customer projects. The secure backend is used to view and edit all data and enables data exchange between ERP and COSYS. Access our hardware expertise in points smartphones and MDE devices.
Warehouse management software from COSYS
Clear warehouse management is important for both wholesalers and craft businesses. Inconsistent stock levels, excess quantities and shortages always lead to extra work, customer dissatisfaction, unnecessary capital commitment in the form of storage space and ultimately only cause extra costs. To avoid these additional costs and at the same time work faster, use COSYS warehouse management software.
Every software needsHardware. In some cases, business smartphones are sufficient as MDE devices for small companies, which achieve a high scanning performance with COSYS Scan Plugin. Much more robust and, thanks to accessories, more ergonomic are full-fledged MDE devices such as the Zebra TC52x/TC57x or the Honeywell EDA71. Both are full-touch devices, with a comfortable display size. The Zebra device is more robust and modern in many respects, for example with the more up-to-date Android 10 version. In return, the Honeywell scores in price.
The wholesale trade assembles its warehouse management software. COSYS already has standardized software modules such as goods receipt, putaway, stock transfer, picking, packing and shipping or inventory. Depending on which processes you want to map, we add the appropriate modules.
Once you have decided on modules, it is a matter of customizing the module masks so that all the data that is important to you is recorded. This includes batches, serial numbers, opened quantities or weight. If you run a chaotic warehouse, we also store a field in the software for free entry of storage bins to move items in, out or around. Many customers want the software to show the employee in which storage bins the scanned item is already located, in order to keep like with like.
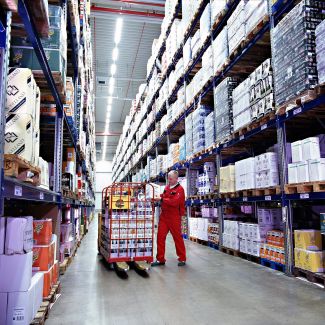
For the warehouse master theCOSYS WebDesk a helpful tool for setting priorities for jobs, splitting jobs or assigning them directly to employees. You can also manage users and locations in WebDesk. If you offer a consignment warehouse, for example, you assign this warehouse its own client and view the stocks separately. As soon as the customer removes goods from the consignment warehouse, WebDesk automatically generates repeat orders and picking orders for this client.
We make data exchange between the ERP system and COSYS software possible in many ways: file imports, data exchange tables, file interfaces, etc.. These interfaces ensure that the mobile application always has the latest master data, orders and purchase orders and the ERP system has the real-time inventories.
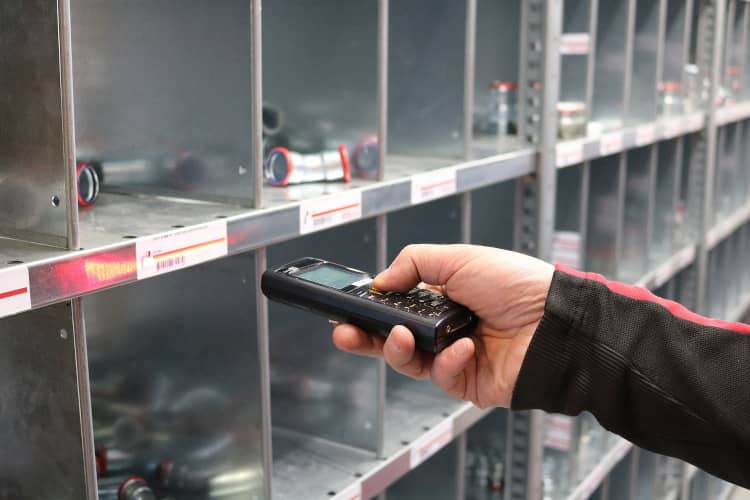
In craft businesses, it´s all about driving to the customer with the right goods to complete all repairs, installations and maintenance in one go. If you track all goods receipts, stock transfers and goods issues, you not only keep the inventories clean, you can also see which item was delivered to which customer, document damage and define minimum stock levels.
In the standard version, the mobile application for inventory management has two modules: Goods Receiving and Picking. For some craft businesses it is worth adding the module Stock Transfer. With stock transfer, you move items from the warehouse to the vehicle. For example, if it is not sure which items
necessary for the orders, you simply load everything that comes into question, book the used items to the customer and the unused ones you put back into storage at the end of the day.
Basically, it is important to make warehousing as simple as possible in order to focus on the core business. COSYS assures you of efficient warehousing by changing something here and there in the standard of the software. For a first insight into our solution we have aDemo app in which you can discover the goods receipt and picking modules free of charge. At the same time, test whether mobile data capture with smartphones is something for you.
Do you manufacture or produce special products? Then track the steps from the delivery of the raw material to partial productions to the final product. The mobile documentation provides a complete track and trace and ensures that the notification of completion is not delayed and that the in-house transport receives and delivers the desired goods. COSYS mobile app records the following data: Components, Kanban, Production Orders, Batches and Direct part marking.
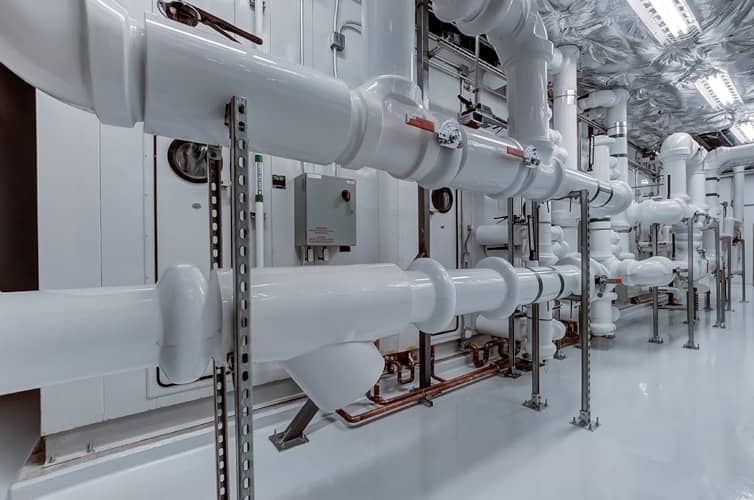
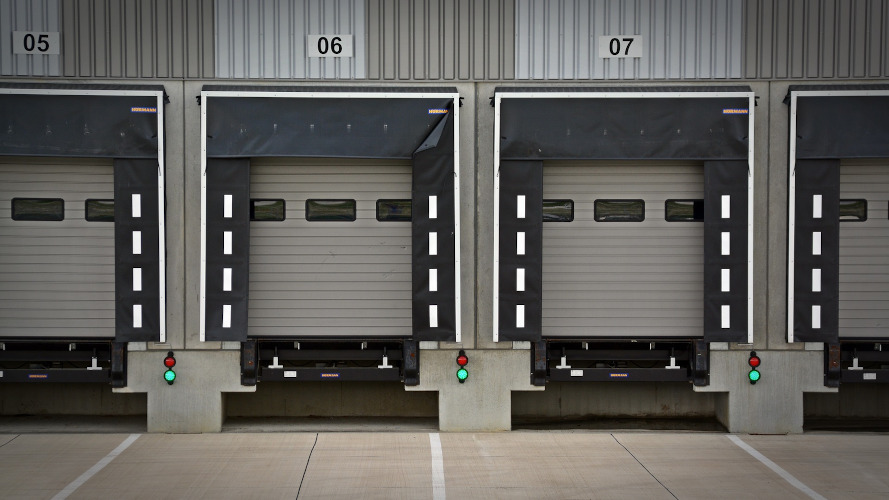
If you are a wholesaler supplying craftsmen´s businesses and construction sites yourself, you need both organized warehouse management and a suitable Transportation Management System. Losses, incorrect deliveries, self-inflicted returns and untraceable damage make transportation an expensive affair. You can solve these problems in one fell swoop with COSYS Transportation Management System.
Take the opportunity and use COSYS hardware service. Our hardware customers come to us for advice on new devices, for repairs, device management and other services such as used devices or old devices as a down payment. As an alternative to purchasing, you can lease MDE devices permanently from us and ensure long-lasting devices with agreements on various hardware services and protect yourself against failures.
Load pipes, fasteners or cleaners for construction sites at your central warehouse conveniently via the Tours module. The scan of the individual packages ensures that all packages planned for the tour are loaded in the correct quantity. Alternatively, scan an NVE if your warehouse works with it. The NVE enables faster processes both at the loading bay and during delivery. Your own craftsmen handle assemblies? Document via a scan which components your craftsmen assemble at customers.
If the place of delivery is agreed with the customer, the driver places the ordered goods there. By scanning the goods, he ensures that the customer receives his ordered goods. Error messages indicate any incorrect entries. Since construction site deliveries are seldom accepted personally by the customer, simply document the proper delivery via a photo. Some customers also want the driver to confirm the delivery on the MDE device. If desired, COSYS software sends an automatic notification that the goods are now on site.
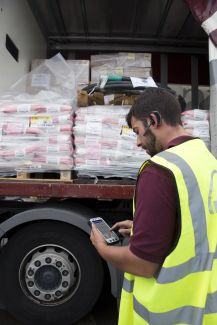
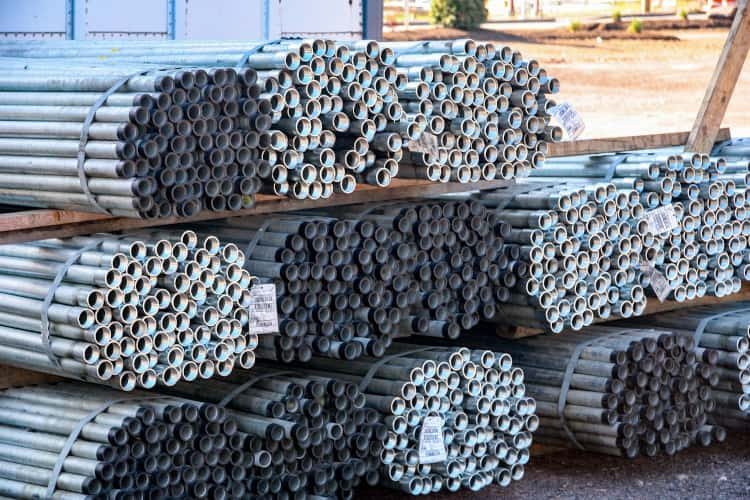
Small craft businesses order only very few items in stock so as not to overload the limited storage space. Short-term and urgent orders on mixed pallets are therefore the order of the day. COSYS mobile tours app shows the driver the tour stops, customers and packages to be loaded for each tour. The driver only has to scan, load and deliver. In case of wrong entries, the driver receives an audible error message on his MDE device. When delivery is complete, the customer signs on the MDE device.
Shipping or self-pickup? If customers pick up goods from you themselves, we map this via the Self-pickup module. If a customer has decided on something on site and it is now ready to be picked, the employee at goods issue simply opens the self-pickup module, scans the individual packages or an NVE and has the customer countersign the pickup.
If you use COSYS Transport Management System and run your tours with it, we can simply add a field for Loading equipment management. During loading and delivery, the driver documents the loading equipment for the tour via drop-down or scan of serial numbers. This way you can see in the back office how many loading equipment are on which tour and how many are with which customer. If you use serial numbers, you not only know how many loading devices are where, but also which ones.
You need a solution purely to manage load carriers, containers, boxes, pallets, etc.? COSYS also has a software explicitly for loading equipment management, which enables a complete track and trace of all loading equipment including photo documentation. If you also provide your loading equipment with serial numbers, you can see in the COSYS WebDesk which loading equipment is where: in the warehouse, at the customer, on a tour? The mobile app has two modules: Retrieval and Storage, in which the loading equipment is recorded and booked via drop-down or barcode scan.
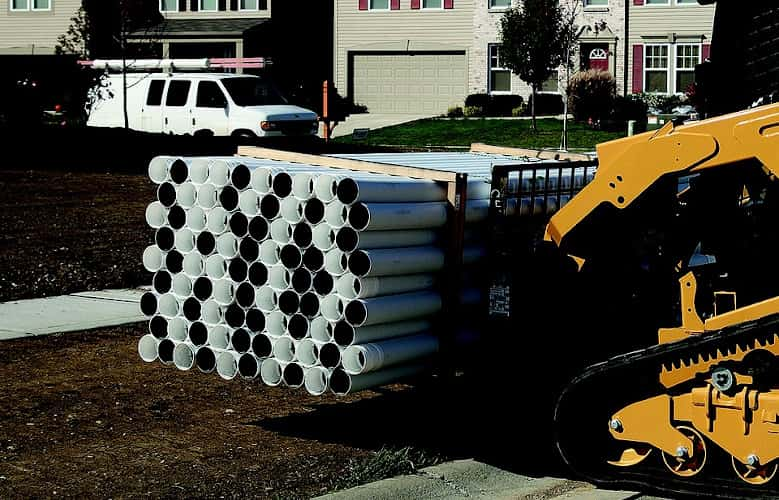
There is a possibility to test COSYS Loading equipment management by yourself for free. Go to the Google Play Store or Apple App Store with your smartphone and install Loading equipment managementCloud Demo. Credentials are not required, just open and start.
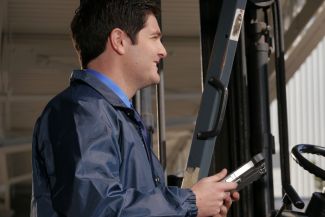
Reordering goods is often more difficult than it should be. Either the reordering is only possible via complicated ways in the ERP system, whereby only the systemically maintained stocks are taken into account, or the internal structure and hierarchy causes detours. In any case, you can remedy the situation with COSYS Software Online Order. The mobile software accesses the data in the ERP system via interfaces and thus exchanges data between the two systems. Depending on the process, the employee uses the order entry or purchase order with order proposal module.
The "Enter order" module regulates mobile reordering. The employee first looks in the warehouse or on site to see what is missing. Is an article out or as good as,
he deposits an order number in the first field, then scans the article number and enters the quantity to be ordered. Comments on the order are optional. When the user taps on Complete, the order is transferred to an ERP system or other customer systems. If intermediaries need to approve the order first, this can also be handled digitally.
In the "Purchase order with order proposal" module, purchase orders created in the ERP system are checked on site and corrected if necessary. A check is useful if systemic and physical data do not always match or if stocks change constantly due to short turnaround times. The software shows the employee the pending orders on the MDE device. He selects an order, which takes him to an overview of the items to be ordered and allows him to release, correct or reject the order.
Inventory
Software: You are dissatisfied with the current Inventory? No matter how large or diverse your assortment is, COSYS software guides your employees through the inventory in an organized and structured way. Pre-determined count locations are scanned first. Then the items follow either via 1 scan = quantity 1 or the employee counts how many pipes, taps etc. are on the counting place per item number. Before the employee completes a counting place, he can check the inventory via an overview and correct it if necessary.
Inventory data:Once all counting stations have been recorded, the employee sends the data to the COSYS backend. This means that the collection can be done completely offline. Most customers want to have the inventory data sent to a leading system (ERP). We provide this data transfer via interfaces, for example file exports or data exchange tables. Alternatively or additionally, you create an inventory log via the COSYS WebDesk user interface, which you store for yourself and the auditor.
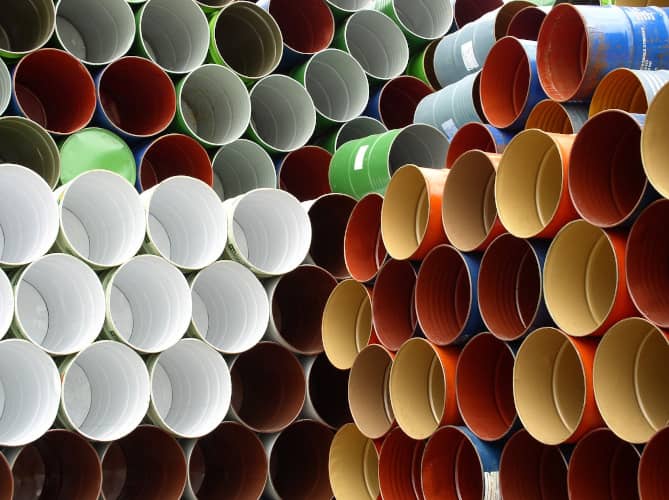
HardwareYou are missing hardware? Then borrow your missing MDE devices or smartphones from us to equip each employee with a handheld for inventory. Our technical department repairs alternatively your current devices. If hardware is generally missing, COSYS sells and leases various MDE devices - new or used - and has longstanding partnerships with manufacturers such as Zebra, Datalogic or Honeywell.
View loading lists, inventory overviews, ordering, etc. on the go
Cloud and on premise backend including user interface
Set up automatic email notifications
Capture batches, serial numbers and photos digitally
Error messages in case of incorrect acquisition
almost error-free work
easy introduction of the COSYS system
Mobile app guides employees through processes in a time-saving manner
Employees and customers are always up to date
specific SHK data are also documented
Wholesale plumbing supplies / building materials trade complete solution
COSYS offers a wide range of solutions for companies in the HVAC industry. The large selection of software modules offers the possibility to digitalize and transparently design every work step along the supply chain.
Production solutions
Component tracing
Production order info
Bearing solutions
Warehouse Management Software
Batch management
Inventory / Inventory
Evaluation
Transport solutions
Tours
Shipping and collection
Loading equipment management
Fleet Management
FAQs in the wholesale plumbing / building materials trade
Yes. Our software can work with all the data that we receive from our customers. You just have to decide in a workshop how the collection should be done.
Yes, for example, if you are dealing with material ordered in kilos or meters, COSYS software shows not only the item number and storage location, but also how much of the item is still available.
Yes, the COSYS WebDesk administration interface offers the possibility to create clients for each location. This also includes, for example, consignment warehouses.
No. The mobile software and the COSYS WebDesk can be operated intuitively. We also host the data for you in a cloud. To hand over complete responsibility, secure further support from COSYS with a software maintenance contract.
Interested? Request a quote from our sales department today at +49 5062 900 0 or via our contact form.
Contact form